Design for Automotive EMC Compliance
Description
Today's automobiles are complex electronic systems containing dozens of microprocessors and a variety of RF transmitters and receivers. Keeping track of all possible interactions that might result in an electromagnetic interference problem can be a formidable task. Nevertheless, it is possible to design components and systems in a manner that guarantees automotive EMC requirements will be met the first time a component or vehicle is brought into the lab for testing.
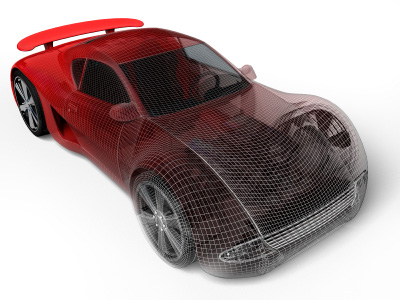
First-pass compliance with automotive EMC requirements starts with circuit board layout. Printed circuit board layout is often the single most important factor affecting the electromagnetic compatibility of electronic systems. Boards that are auto-routed or laid out according to a list of “design rules” do not usually meet electromagnetic compatibility requirements on the first pass; and the products using these boards are more likely to require expensive EMC “fixes” such as ferrites on cables and shielded enclosures. Taking the time to ensure that components are properly placed, transition times are not left to chance, and traces are optimally routed will generally result in products that meet all electromagnetic compatibility and signal integrity requirements on time and on budget.
Automotive components rarely employ shielded enclosures and are subjected to a unique set of EMC tests that can be difficult to comply with unless specific design precautions are implemented early in a product's development. For example, products designed to route high-frequency currents on cables to a low-impedance chassis ground readily meet bulk current injection (BCI) requirements; while products that do not provide for this in the initial board layout may require expensive fixes to meet the same requirements. Compliance with radiated emissions requirements can also be relatively straight-forward when signal transition times are controlled and care is taken to avoid design mistakes that allow high-frequency noise currents to flow onto a cable harness.
Most automotive components employ mixed-signal boards (boards with both analog and digital circuits). Mixed-signal boards in automotive applications require that special attention be paid to the routing of the low-frequency analog currents. Minor mistakes in the layout of these boards can make the difference between a reliable product and a product with severe susceptibility problems.
Decisions related to wire harness design and routing can have a profound effect on a vehicle's electromagnetic compatibility. The course will present overall strategies for vehicle-level design, including component characterization for vehicle-level modeling and system interactions that must be accounted for early in the automotive design process.
This course stresses the fundamental concepts and tools that automotive electronics engineers can utilize to avoid electromagnetic compatibility and signal integrity problems. Students completing the course will be able to make good decisions regarding board layout and automotive system design for EMC. They will also be introduced to tools and techniques for quickly reviewing automotive designs in order to flag potential problems well before the first hardware is built and tested.
Continuing Education Credit: 1.5 CEUs, 15 PDHs
Course Outline
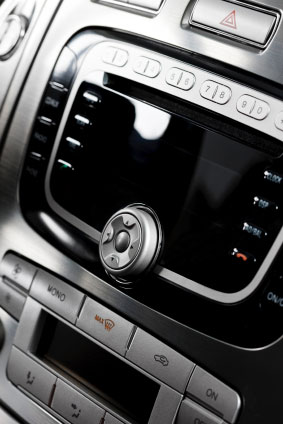
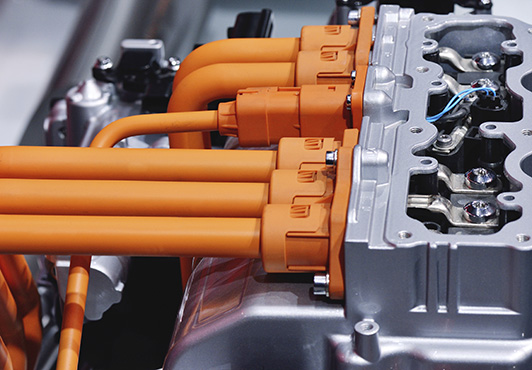
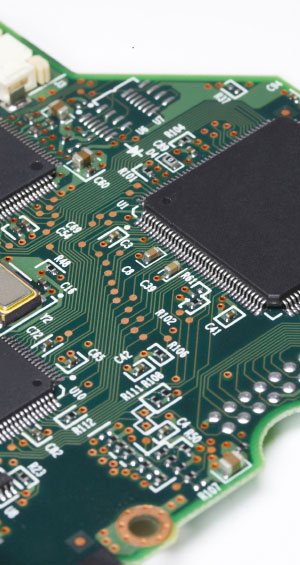
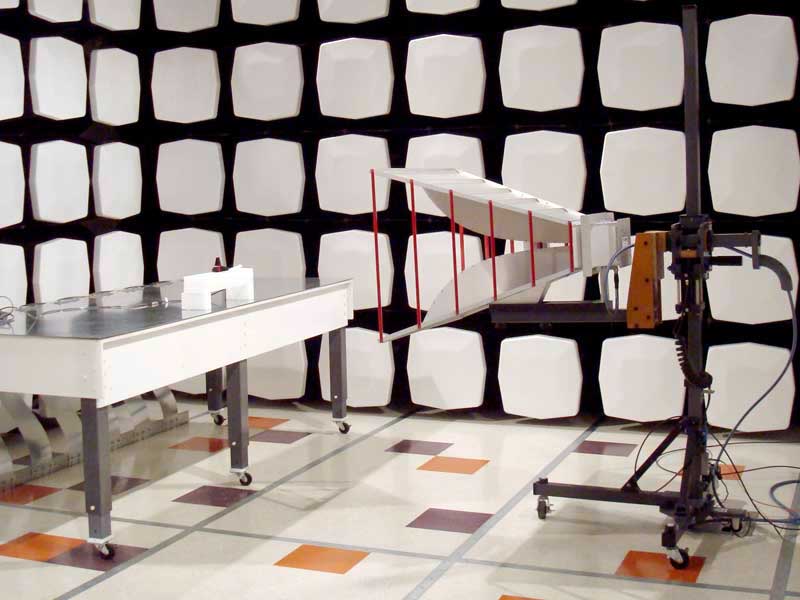
Part 1 - Important Fundamental Concepts
- Introduction
- Automotive Components and Systems
- Automotive EMC Requirements
- Impact of Layout on Product Compliance and Cost
- Examples of Good and Bad Designs
- Signal Routing and Termination
- Tracing Current Paths / Concept of Least Impedance
- Transition Time Control
- Transmission Lines
- Balanced or Unbalanced
- Identifying Unintentional Antennas/Ports
- Essential Elements of an Antenna
- The Wire Harness
- The Chassis/Enclosure
- Noise Sources and Coupling Mechanisms
- Integrated Circuits as Sources of EMI
- Common Automotive Noise Sources
- ESD and Transient Susceptibility
- Conducted, Electric and Magnetic Field Coupling
- Grounding
- Ground vs. Signal Return
- Ground Structures and Grounding Conductors
- Utilizing Vehicle Ground
- Ground in Mixed-Signal Environments
- Filtering
- Insertion Loss
- First-Order Low-Pass Filters
- Second-Order Low-Pass Filters
- Component Parasitics
- Shielding
- Electric Field Shielding
- Magnetic Field Shielding
- Shielding to Reduce Radiated Emissions
- Cable Shielding
Part 2 - Design Tools and Techniques
- Strategies for PCB Layout
- Design Guidelines (Good and Bad)
- Optimizing Component Placement
- Stack-up and Routing Priorities
- Common Problems that are Easily Avoided
- Strategies for Vehicle Layout
- Design Guidelines (Good and Bad)
- Optimizing Component Placement
- Wire Harness Design and Routing
- Common Problems that are Easily Avoided
- Key Design Considerations
- For Radiated Emissions Tests
- For Conducted Emissions Tests
- For BCI and Radiated Susceptibility
- For ESD and Transient Tests
- Design Review Steps and Examples
- Identifying Sources/Victims
- Identifying Antennas/Ports
- Applying Design Guidelines/Criteria
- Tools of the Trade
- Schematic and Board Layout Tools
- Circuit Solvers
- Field Solvers
- Full-Wave Modeling Tools
- Design Rule Checkers
- Maximum Emissions/Coupling Calculators
- Specific Design Examples
- Engine Control Module
- Body Control Module
- Infotainment System
- Power Inverter / Motor Driver
- Course Summary
- Review of Key Concepts
- Resources for Automotive EMC Engineers
Course Instructor
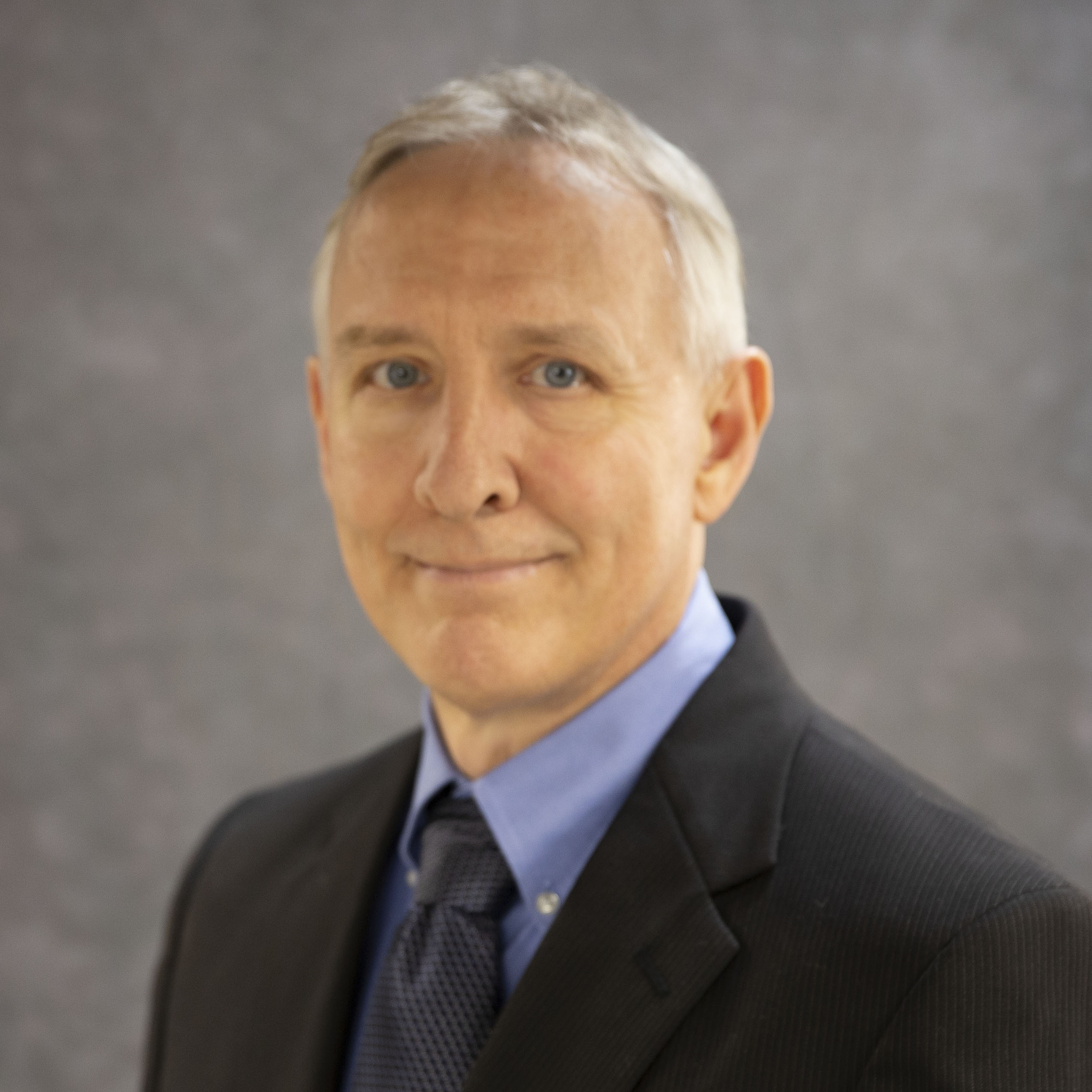
Dr. Todd H. Hubing is a Professor Emeritus of Electrical and Computer Engineering at Clemson University and former Director of the Clemson Vehicular Electronics Laboratory. He has contributed to the development and analysis of hundreds of automotive electronic components and systems. At Clemson, he and his students were able to guarantee that the products they reviewed would meet all automotive EMC requirements on the first test pass. They were able to make this guarantee by applying the concepts outlined in this course along with simple tools to calculate the maximum possible coupling from various components and circuits. Instead of applying general design guidelines that may or may not be helpful in a given situation, this approach makes it possible to identify exactly what is necessary to ensure product compliance.